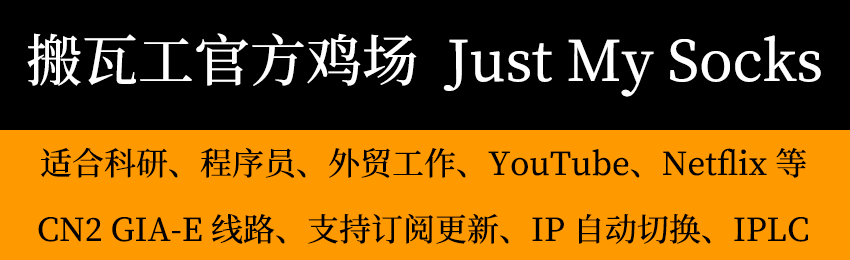
电子器件是一个非常复杂的系统,其封装过程的缺陷和失效也是非常复杂的。因此,研究封装缺陷和失效需要对封
电子器件是一个非常复杂的系统,其封装过程的缺陷和失效也是非常复杂的。因此,研究封装缺陷和失效需要对封装过程有一个系统性的了解,这样才能从多个角度去分析缺陷产生的原因。
封装缺陷与失效的研究方法论
封装的失效机理可以分为两类:过应力和磨损。
过应力失效往往是瞬时的、灾难性的;磨损失效是长期的累积损坏,往往首先表示为性能退化,接着才是器件失效。失效的负载类型又可以分为机械、热、电气、辐射和化学负载等。
影响封装缺陷和失效的因素是多种多样的, 材料成分和属性、封装设计、环境条件和工艺参数等都会有所影响。确定影响因素是预防封装缺陷和失效的基本前提。
影响因素可以通过试验或者模拟仿真的方法来确定,一般多采用物理模型法和数值参数法。对于更复杂的缺陷和失效机理,常常采用试差法确定关键的影响因素,但是这个方法需要较长的试验时间和设备修正,效率低、花费高。
在分析失效机理的过程中, 采用鱼骨图(因果图)展示影响因素是行业通用的方法。鱼骨图可以说明复杂的原因及影响因素和封装缺陷之间的关系,也可以区分多种原因并将其分门别类。
生产应用中,有一类鱼骨图被称为6Ms:从机器、方法、材料、量度、人力和自然力等六个维度分析影响因素。
这一张图所示的是展示塑封芯片分层原因的鱼骨图,从设计、工艺、环境和材料四个方面进行了分析。通过鱼骨图,清晰地展现了所有的影响因素,为失效分析奠定了良好基础。
引发失效的负载类型
如上一节所述,封装的负载类型可以分为机械、热、电气、辐射和化学负载。
1. 失效机理的分类
机械载荷:包括物理冲击、振动、填充颗粒在硅芯片上施加的应力(如收缩应力)和惯性力(如宇宙飞船的巨大加速度)等。材料对这些载荷的响应可能表现为弹性形变、塑性形变、翘曲、脆性或柔性断裂、界面分层、疲劳裂缝产生和扩展、蠕变以及蠕变开裂等等。
热载荷:包括芯片黏结剂固化时的高温、引线键合前的预加热、成型工艺、后固化、邻近元器件的再加工、浸焊、气相焊接和回流焊接等等。外部热载荷会使材料因热膨胀而发生尺寸变化,同时也会改变蠕变速率等物理属性。如发生热膨胀系数失配(CTE失配)进而引发局部应力,并最终导致封装结构失效。过大的热载荷甚至可能会导致器件内易燃材料发生燃烧。
电载荷:包括突然的电冲击、电压不稳或电流传输时突然的振荡(如接地不良)而引起的电流波动、静电放电、过电应力等。这些外部电载荷可能导致介质击穿、电压表面击穿、电能的热损耗或电迁移。也可能增加电解腐蚀、树枝状结晶生长,引起漏电流、热致退化等。
化学载荷:包括化学使用环境导致的腐蚀、氧化和离子表面枝晶生长。由于湿气能通过塑封料渗透,因此在潮湿环境下湿气是影响塑封器件的主要问题。
被塑封料吸收的湿气能将塑封料中的催化剂残留萃取出来,形成副产物进入芯片粘接的金属底座、半导体材料和各种界面,诱发导致器件性能退化甚至失效。
例如,组装后残留在器件上的助焊剂会通过塑封料迁移到芯片表面。在高频电路中,介质属性的细微变化(如吸潮后的介电常数、耗散因子等的变化)都非常关键。在高电压转换器等器件中,封装体击穿电压的变化非常关键。
此外,一些环氧聚酰胺和聚氨酯如若长期暴露在高温高湿环境中也会引起降解(有时也称为“逆转”)。通常采用加速试验来鉴定塑封料是否易发生该种失效。
需要注意的是,当施加不同类型载荷的时候,各种失效机理可能同时在塑封器件上产生交互作用。
例如,热载荷会使封装体结构内相邻材料间发生热膨胀系数失配,从而引起机械失效。其他的交互作用,包括应力辅助腐蚀、应力腐蚀裂纹、场致金属迁移、钝化层和电解质层裂缝、湿热导致的封装体开裂以及温度导致的化学反应加速等等。在这些情况下,失效机理的综合影响并不一定等于个体影响的总和。
封装缺陷的分类
封装缺陷主要包括引线变形、底座偏移、翘曲、芯片破裂、分层、空洞、不均匀封装、毛边、外来颗粒和不完全固化等。
1. 引线变形
引线变形通常指塑封料流动过程中引起的引线位移或者变形,通常采用引线最大横向位移x与引线长度L之间的比值x/L来表示。引线弯曲可能会导致电器短路(特别是在高密度I/O器件封装中)。有时,弯曲产生的应力会导致键合点开裂或键合强度下降。
影响引线键合的因素包括封装设计、引线布局、引线材料与尺寸、模塑料属性、引线键合工艺和封装工艺等。影响引线弯曲的引线参数包括引线直径、引线长度、引线断裂载荷和引线密度等等。
2. 底座偏移
底座偏移指的是支撑芯片的载体(芯片底座)出现变形和偏移。
如图所示为塑封料导致的底座偏移,此时,上下层模塑腔体内不均匀的塑封料流动会导致底座偏移。
影响底座偏移的因素包括塑封料的流动性、引线框架的组装设计以及塑封料和引线框架的材料属性。薄型小尺寸封装(TSOP)和薄型方形扁平封装(TQFP)等封装器件由于引线框架较薄,容易发生底座偏移和引脚变形。
3. 翘曲
翘曲是指封装器件在平面外的弯曲和变形。因塑封工艺而引起的翘曲会导致如分层和芯片开裂等一系列的可靠性问题。翘曲也会导致一系列的制造问题,如在塑封球栅阵列(PBGA)器件中,翘曲会导致焊料球共面性差,使器件在组装到印刷电路板的回流焊过程中发生贴装问题。
翘曲模式包括内凹、外凸和组合模式三种
导致翘曲的原因主要包括CTE失配和固化/压缩收缩。后者一开始并没有受到太多的关注,深入研究发现,模塑料的化学收缩在IC器件的翘曲中也扮演着重要角色,尤其是在芯片上下两侧厚度不同的封装器件上。在固化和后固化的过程中,塑封料在高固化温度下将发生化学收缩,被称为“热化学收缩”。通过提高玻璃化转变温度和降低Tg附近的热膨胀系数变化,可以减小固化过程中发生的化学收缩。
导致翘曲的因素还包括诸如塑封料成分、模塑料湿气、封装的几何结构等等。通过对塑封材料和成分、工艺参数、封装结构和封装前环境的把控,可以将封装翘曲降低到最小。在某些情况下,可以通过封装电子组件的背面来进行翘曲的补偿。例如,大陶瓷电路板或多层板的外部连接位于同一侧,对他们进行背面封装可以减小翘曲。
4. 芯片破裂
封装工艺中产生的应力会导致芯片破裂。封装工艺通常会加重前道组装工艺中形成的微裂缝。晶圆或芯片减薄、背面研磨以及芯片粘结都是可能导致芯片裂缝萌生的步骤。
破裂的、机械失效的芯片不一定会发生电气失效。芯片破裂是否会导致器件的瞬间电气失效还取决于裂缝的生长路径。例如,若裂缝出现在芯片的背面,可能不会影响到任何敏感结构。
因为硅晶圆比较薄且脆,晶圆级封装更容易发生芯片破裂。因此,必须严格控制转移成型工艺中的夹持压力和成型转换压力等工艺参数,以防止芯片破裂。3D堆叠封装中因叠层工艺而容易出现芯片破裂。在3D封装中影响芯片破裂的设计因素包括芯片叠层结构、基板厚度、模塑体积和模套厚度等。
5. 分层
分层或粘结不牢指的是在塑封料和其相邻材料界面之间的分离。分层位置可能发生在塑封微电子器件中的任何区域;同时也可能发生在封装工艺、后封装制造阶段或者器件使用阶段。
封装工艺导致的不良粘接界面是引起分层的主要因素。界面空洞、封装时的表面污染和固化不完全都会导致粘接不良。其他影响因素还包括固化和冷却时收缩应力与翘曲。在冷却过程中,塑封料和相邻材料之间的CTE不匹配也会导致热-机械应力,从而导致分层。
可以根据界面类型对分层进行分类
6. 空洞
封装工艺中,气泡嵌入环氧材料中形成了空洞,空洞可以发生在封装工艺过程中的任意阶段,包括转移成型、填充、灌封和塑封料至于空气环境下的印刷。通过最小化空气量,如排空或者抽真空,可以减少空洞。有报道采用的真空压力范围为1~300Torr(一个大气压为760Torr)。
填模仿真分析认为,是底部熔体前沿与芯片接触,导致了流动性受到阻碍。部分熔体前沿向上流动并通过芯片外围的大开口区域填充半模顶部。新形成的熔体前沿和吸附的熔体前沿进入半模顶部区域,从而形成起泡。
7. 不均匀封装
非均匀的塑封体厚度会导致翘曲和分层。传统的封装技术,诸如转移成型、压力成型和灌注封装技术等,不易产生厚度不均匀的封装缺陷。晶圆级封装因其工艺特点,而特别容易导致不均匀的塑封厚度。
为了确保获得均匀的塑封层厚度,应固定晶圆载体使其倾斜度最小以便于刮刀安装。此外,需要进行刮刀位置控制以确保刮刀压力稳定,从而得到均匀的塑封层厚度。
在硬化前,当填充粒子在塑封料中的局部区域聚集并形成不均匀分布时,会导致不同质或不均匀的材料组成。塑封料的不充分混合将会导致封装灌封过程中不同质现象的发生。
8. 毛边
毛边是指在塑封成型工艺中通过分型线并沉积在器件引脚上的模塑料。
夹持压力不足是产生毛边的主要原因。如果引脚上的模料残留没有及时清除,将导致组装阶段产生各种问题。例如,在下一个封装阶段中键合或者黏附不充分。树脂泄漏是较稀疏的毛边形式。
9. 外来颗粒
在封装工艺中,封装材料若暴露在污染的环境、设备或者材料中,外来粒子就会在封装中扩散并聚集在封装内的金属部位上(如IC芯片和引线键合点),从而导致腐蚀和其他的后续可靠性问题。
10. 不完全固化
固化时间不足或者固化温度偏低都会导致不完全固化。另外,在两种封装料的灌注中,混合比例的轻微偏移都将导致不完全固化。为了最大化实现封装材料的特性,必须确保封装材料完全固化。在很多封装方法中,允许采用后固化的方法确保封装材料的完全固化。而且要注意保证封装料比例的精确配比。
封装失效的分类
在封装组装阶段或者器件使用阶段,都会发生封装失效。特别是当封装微电子器件组装到印刷电路板上时更容易发生,该阶段器件需要承受高的回流温度,会导致塑封料界面分层或者破裂。
1. 分层
如上一节所述,分层是指塑封材料在粘接界面处与相邻的材料分离。可能导致分层的外部载荷和应力包括水汽、湿气、温度以及它们的共同作用。
在组装阶段常常发生的一类分层被称为水汽诱导(或蒸汽诱导)分层,其失效机理主要是相对高温下的水汽压力。
在封装器件被组装到印刷电路板上的时候,为使焊料融化温度需要达到220℃甚至更高,这远高于模塑料的玻璃化转变温度(约110~200℃)。
在回流高温下,塑封料与金属界面之间存在的水汽蒸发形成水蒸气,产生的蒸汽压与材料间热失配、吸湿膨胀引起的应力等因素共同作用,最终导致界面粘接不牢或分层,甚至导致封装体的破裂。
无铅焊料相比传统铅基焊料,其回流温度更高,更容易发生分层问题。
2. 吸湿膨胀系数(CHE),又称湿气膨胀系数(CME)
湿气扩散到封装界面的失效机理是水汽和湿气引起分层的重要因素。
湿气可通过封装体扩散,或者沿着引线框架和模塑料的界面扩散。研究发现,当模塑料和引线框架界面之间具有良好粘接时,湿气主要通过塑封体进入封装内部。
但是,当这个粘结界面因封装工艺不良(如键合温度引起的氧化、应力释放不充分引起的引线框架翘曲或者过度修剪和形式应力等)而退化时,在封装轮廓上会形成分层和微裂缝,并且湿气或者水汽将易于沿这一路径扩散。
更糟糕的是,湿气会导致极性环氧黏结剂的水合作用,从而弱化和降低界面的化学键合。
表面清洁是实现良好粘结的关键要求。表面氧化常常导致分层的发生(如上一篇中所提到的例子),如铜合金引线框架暴露在高温下就常常导致分层。氮气或其他合成气体的存在,有利于避免氧化。
模塑料中的润滑剂和附着力促进剂会促进分层。润滑剂可以帮助模塑料与模具型腔分离,但会增加界面分层的风险。另一方面,附着力促进剂可以确保模塑料和芯片界面之间的良好粘结,但却难以从模具型腔内清除。
分层不仅为水汽扩散提供了路径,也是树脂裂缝的源头。分层界面是裂缝萌生的位置,当承受交大外部载荷的时候,裂缝会通过树脂扩展。
研究表明,发生在芯片底座地面和树脂之间的分层最容易引起树脂裂缝,其它位置出现的界面分层对树脂裂缝的影响较小。
3. 气相诱导裂缝(爆米花现象)
水汽诱导分层进一步发展会导致气相诱导裂缝。当封装体内水汽通过裂缝逃逸时会产生爆裂声,和爆米花的声音非常像,因此又被称为爆米花现象。
裂缝常常从芯片底座向塑封底面扩展。在焊接后的电路板中,外观检查难以发现这些裂缝。QFP和TQFP等大而薄的塑封形式最容易产生爆米花现象;此外也容易发生在芯片底座面积与器件面积之比较大、芯片底座面积与最小塑封料厚度之比较大的的器件中。
爆米花现象可能会伴随其他问题,包括键合球从键合盘上断裂以及键合球下面的硅凹坑等。
塑封器件内的裂缝通常起源于引线框架上的应力集中区(如边缘和毛边),并且在最薄塑封区域内扩展。毛边是引线框架表面在冲压工艺中产生的小尺寸变形,改变冲压方向使毛边位于引线框架顶部,或者刻蚀引线框架(模压)都可以减少裂缝。
减少塑封器件内的湿气是降低爆米花现象的关键。常采用高温烘烤的方法减少塑封器件内的湿气。前人研究发现,封装内允许的安全湿气含量约为1100×10^-6(0.11 wt.%)。在125℃下烘烤24h,可以充分去除封装内吸收的湿气。
4. 脆性断裂
脆性断裂经常发生在低屈服强度和非弹性材料中(如硅芯片)。到材料受到过应力作用时,突然的、灾难性的裂缝扩展会起源于如空洞、夹杂物或不连续等微小缺陷。
5. 韧性断裂
塑封材料容易发生脆性和韧性两种断裂模式,主要取决于环境和材料因素,包括温度、聚合树脂的黏塑特性和填充载荷。
即使在含有脆性硅填料的高加载塑封材料中,因聚合树脂的黏塑特性,仍然可能发生韧性断裂。
6. 疲劳断裂
塑封料遭受到极限强度范围内的周期性应力作用时,会因累积的疲劳断裂而断裂。
施加到塑封材料上的湿、热、机械或综合载荷,都会产生循环应力。疲劳失效是一种磨损失效机理,裂缝一般会在间断点或缺陷位置萌生。
疲劳断裂机理包括三个阶段:裂纹萌生(阶段Ⅰ);稳定的裂缝扩展(阶段Ⅱ);突发的、不确定的、灾难性失效(阶段Ⅲ)。在周期性应力下,阶段Ⅱ的疲劳裂缝扩展指的是裂缝长度的稳定增长。塑封材料的裂纹扩展速率要远高于金属材料疲劳裂缝扩展的典型值(约3倍)。
7. 加速失效的因素
环境和材料的载荷和应力,如湿气、温度和污染物,会加速塑封器件的失效。
塑封工艺正在封装失效中起到了关键作用,如湿气扩散系数、饱和湿气含量、离子扩散速率、热膨胀系数和塑封材料的吸湿膨胀系数等特性会极大地影响失效速率。
导致失效加速的因素主要有潮气、温度、污染物和溶剂性环境、残余应力、自然环境应力、制造和组装载荷以及综合载荷应力条件。
潮气 能加速塑封微电子器件的分层、裂缝和腐蚀失效。在塑封器件中, 潮气是一个重要的失效加速因子。
与潮气导致失效加速有关的机理包括粘结面退化、吸湿膨胀应力、水汽压力、离子迁移以及塑封料特性改变等等。潮气能够改变塑封料的玻璃化转变温度Tg、弹性模量和体积电阻率等特性。
温度 是另一个关键的失效加速因子,通常利用与模塑料的玻璃化转变温度、各种材料的热膨胀洗漱以及由此引起的热-机械应力相关的温度等级来评估温度对封装失效的影响。
温度对封装失效的另一个影响因素表现在会改变与温度相关的封装材料属性、湿气扩散系数和金属间扩散等失效。
污染物和溶剂性环境 污染物为失效的萌生和扩展提供了场所,污染源主要有大气污染物、湿气、助焊剂残留、塑封料中的不洁净例子、热退化产生的腐蚀性元素以及芯片黏结剂中排出的副产物(通常为环氧)。
塑料封装体一般不会被腐蚀,但是湿气和污染物会在塑封料中扩散并达到金属部位,引起塑封器件内金属部分的腐蚀。
残余应力 芯片粘结会产生单于应力。应力水平的大小,主要取决于芯片粘接层的特性。由于模塑料的收缩大于其他封装材料, 因此模塑成型时产生的应力是相当大的。可以采用应力测试芯片来测定组装应力。
自然环境应力 在自然环境下,塑封料可能会发生降解。降解的特点是聚合键的断裂,常常是固体聚合物转变成包含单体、二聚体和其他低分子量种类的黏性液体。
升高的温度和密闭的环境常常会加速降解。阳光中的紫外线和大气臭氧层是降解的强有力催化剂,可通过切断环氧树脂的分子链导致降解。
将塑封器件与易诱发降解的环境隔离、采用具有抗降解能力的聚合物都是防止降解的方法。需要在湿热环境下工作的产品要求采用抗降解聚合物。
制造和组装载荷 制造和组装条件都有可能导致封装失效,包括高温、低温、温度变化、操作载荷以及因塑封料流动而在键合引线和芯片底座上施加的载荷。进行塑封器件组装时出现的爆米花现象就是一个典型的例子。
综合载荷应力条件 在制造、组装或者操作的过程中,诸如温度和湿气等失效加速因子常常是同时存在的。综合载荷和应力条件常常会进一步加速失效。这一特点常被应用于以缺陷部件筛选和易失效封装器件鉴别为目的的加速试验设计。
长按二维码关注芯闻天下